If you have soldered before, you might have encountered situations in which the solder doesn’t “want” to stick to the contacts or even flow where you intended. When soldering, any amount of oxidation and impurities can make the process more challenging and even lead to a bad solder joint or poor electrical connection.
That is where soldering flux comes in.
Soldering flux is a substance that helps to remove oxidation and impurities from the metal surfaces and promotes the flow of solder by lowering its surface tension, therefore improving the wetting of the surfaces to be joined.
Altogether, soldering flux helps create a reliable solder joint and simplifies the soldering process. Flux is so helpful that even most solder wires for electronics come with flux in the core of the wire. While it may suffice in most cases, some cases may require additional flux.
After soldering, we might be left with residue from the soldering flux. Should you remove the solder flux residue after soldering? The best practice is to remove soldering flux residue after soldering, but in some cases and with certain fluxes, you can leave soldering flux residue. In rare cases, flux can cause issues for high-frequency signals or high-impedance amplifier applications, and some flux types can corrode the connections if not removed.
To better understand the topic, we will first look at what soldering flux is, why it is used, which flux types require cleaning, and how to clean flux residue.
What is a soldering flux?
Soldering flux is a chemical substance used in the world of soldering to clean and prepare surfaces to be soldered. Its main goal is to remove oxidation and impurities and help the solder flow more smoothly onto the surfaces to be joined. In some cases, it can be challenging to establish and create a robust solder joint, so then we turn to this helpful substance.
To better understand the importance of flux, we can consider glue as an example. If glue is put on a greasy and dusty surface without cleaning it first, the chances of it sticking are very slim. Even if it does stick, it will never hold as well as it could. The same goes for soldering; the solder will only stick if the surface is clean.
But you don’t necessarily need soldering flux in every case as, most commonly, solder wire may already have some flux in its core, also known as Cored Solder Wire, and it can suffice for relatively clean surfaces. Adding more solder can help with more oxidized connections, but additional flux may be necessary in more severe cases.
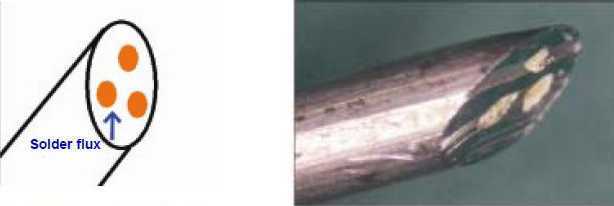
If you are interested in learning more about the different types of fluxes used in electronics, check out our article!
Does soldering flux residue have to be removed?
The best practice is to always clean soldering flux residue, but formally, it depends on which type of flux is used. The more active types of fluxes have a higher risk of becoming corrosive, but all of them can cause issues for digital circuits with high-frequency signals and analog circuits with high-impedance inputs.
Flux residue can increase the interference between digital signals due to leakage currents, which can cause signal integrity issues (more noise – less reliable signal). For high-impedance circuits, flux residue can impact the impedance, which can disturb correct circuit function.
In a more severe case, let’s consider that flux residue is acidic or corrosive, which is the case for more active or aggressive fluxes. Over time, if left on the board, it can corrode the covered metal and ruin the soldered connection and, quite possibly, the PCB along the way.
While no clean flux implies that it is not necessary to clean it, unfortunately, research has shown that no clean flux in lower wave soldering temperatures leaves more residue. Therefore, the acidic part of the flux does not evaporate completely, which can lead to leakage currents and product failures due to corrosion in humid environments. At the same time, ester oils in the residue can make matters worse by collecting dust, which can accumulate moisture. When heat or other chemicals come in contact with the salt activators in the no clean flux, they leave behind white residue, which can corrode the circuit or promote dendrite growth.
To avoid these issues, use no clean flux sparingly and apply heat so that it evaporates completely.
How to clean flux?
The best practice is to take care of the flux residue after soldering. So how can you do it?
In case of no clean and rosin-based fluxes (e.g., RMA), using a flux remover or isopropyl alcohol can be enough. While our team has no personal experience, there are flux remover pens that come in self-sufficient packaging for ease of use. In the case of water-soluble flux, just applying distilled water will do the job. Just make sure to use distilled water instead of tap water, as it contains minerals that can lead to corrosion.
Before you get to work, remember:
-
Work in a well-ventilated area!
-
Exhale while soldering, as that can push the fumes away from your face.
-
Prolonged exposure to soldering fumes can cause eye and throat irritation, among other respiratory problems. Consider using a face mask or a fume extractor to increase protection.
-
Bear in mind that flux remover and isopropyl alcohol are flammable!
-
Avoid skin contact or use gloves, as exposure to these substances can cause dermatitis or skin irritation.
Cleaning procedure:
-
Use a cotton swab or a soft brush and add some flux remover or isopropyl alcohol. I use an old soft toothbrush as they are stiff enough to get the residue but soft enough not to cause damage.
-
Then, with circular motions, clean the affected area. Depending on the severity, the cleaning process should not take too long, but it usually takes a couple of minutes at most.
-
Inspect the cleaned area for leftover flux residue! Repeat if necessary.
-
Make sure to wipe and dry the area!
Beware of online advice to use acetone as flux remover – it can damage plastics and potentially other circuit board components as well!
But if you are really desperate, use acetone at least in lower concentrations than 50%, but use it with caution – test it in small amounts and on small areas first! Either way, we do not recommend doing this!
Conclusion
Depending on the soldering flux used and external factors, flux residue can vary from harmless to causing intermittent electrical issues with more aggressive flux types to even causing damage to the connections or the circuit board. Even if it doesn’t seem necessary to clean at the moment, on rare occasions, it can lead to issues with the proper circuit function, which, in extreme cases, can be dangerous!
So, the best practice is to clean the soldering flux residue! Even if the label says “no clean”, do it anyways! If you are working with no clean flux, use it locally in small amounts and make sure it evaporates when applying heat! The activators in the flux only work when heat is applied! It’s far better to have your circuit work as it should without having any doubts. And it will look much more professional!
We recommend using RMA or no clean flux as they are less aggressive and will do the job in most scenarios. They are the most commonly used types of fluxes for a reason! For added convenience, you can use flux dispensing pens for minor reworks and areas. Make sure you use an appropriate soldering flux for your solder at the recommended temperature, and check out its cleaning requirements!
Thank you for reading our article about cleaning soldering flux residue and why we might want to clean them. If you have any questions, please leave a comment, and we’ll get back to you as soon as possible. Make sure to follow us on social media to keep in touch and learn more about the amazing world of electronics!
Leave a Reply