Most people are familiar with solder as that is the main ingredient and the visible result for creating reliable electrical connections and connecting components to a printed circuit board (PCB). But soldering requires clean surfaces without any oxidation and impurities.
This is where soldering flux comes to save the day! Soldering flux is a chemical substance that cleans and prepares surfaces to be soldered by removing oxidation and impurities and promoting the flow of solder. Some may not even know that solder wire meant for electronics can contain soldering flux in the core of the wire to ensure a reliable and robust solder joint.
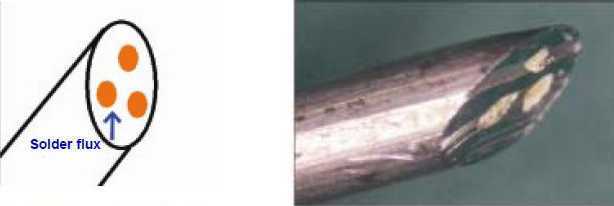
In this article, we will give an overview of the types of most popular and widely used soldering fluxes for electronics and their use cases.
Before we begin, a quick side note:
- Soldering fluxes come in different levels of activity or cleaning ability. While more active fluxes are better at cleaning the surfaces, it comes at a cost – their residue can become corrosive. Therefore, if left uncleaned, it can ruin the soldered connection and even the PCB. For more information, check out our article about flux residue and its effects.
No-Clean flux
No clean flux is the most popular as it, as the name implies, leaves minimal to no traces of residue and, ideally, does not need to be cleaned afterward. This type of flux is most commonly used in small rework cases.
Unfortunately, research has shown that no clean flux in lower wave soldering temperatures leaves more residue. Therefore, the acid part of the flux does not evaporate completely. The leftover acid in the residue can be dissolved into water, leading to leakage currents and product failures in humid environments. Ester oils in the residue can collect dust, which absorbs humidity and further exacerbates the corrosion and leakage currents. When heat or other chemicals come in contact with the salt activators in the no clean flux, they leave behind white residue, which can corrode the circuit or promote dendrite growth.
This means that the same considerations made by the research authors can apply when high amounts of no-clean flux are only locally subjected to heat. Due to these considerations, use no-clean flux sparingly, apply it to the rework area, and ensure it evaporates completely or thoroughly clean it afterward!
The necessity to clean no clean flux is also recognized in the industry. Most manufacturers opt to only clean high-reliability boards, where cleanliness is critical – security, automotive, aerospace, medical devices, etc. By skipping the cleaning process, manufacturers save on labor costs and time but ultimately sacrifice cosmetic appeal and ease of quality assurance for the board.
Either way, the best way to go around this is to clean the flux residue using a flux remover, isopropyl alcohol, or flux-removing pen.
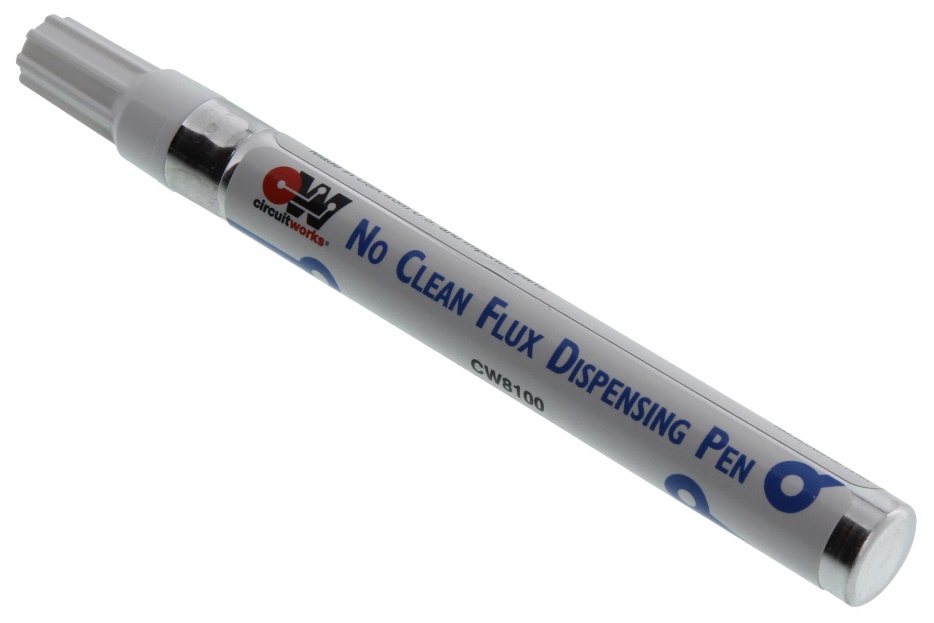
Rosin flux
Rosin flux is an organic flux made from pine resin. Rosin, also known as colophony, has a long history of use, dating back to ancient times, where it was used for various purposes like boat maintenance, making soap, medicine, and much more. Today, it is commonly used to prepare metal surfaces for soldering due to its great oxidant-removing capabilities.
There are three main types of Rosin flux with increasing levels of activity and residue:
- Ordinary Rosin flux (R) – least active and without added activators, therefore, non-corrosive, otherwise known as Non-activated Rosin flux. Leaves little to no residue. Less effective than activated counterparts at cleaning and removing oxide layers;
- Rosin Mildly Activated flux (RMA) – the most commonly used flux due to the balance between less aggressive activators and solderability. The residue is very easy to clean. Arguably, it is the most commonly used flux in electronics besides no clean flux. Recommended for everyday use.
- Rosin Activated flux (RA) – the most aggressive and the most effective. Leaves a lot of residue that can become corrosive if left for an extended period. It must be cleaned after soldering!
Rosin soldering fluxes can be removed using flux remover suitable for the type of flux used or isopropyl alcohol.

Water-Soluble flux
Water-soluble flux is an organic flux that is designed to be cleaned with distilled water. Water-soluble flux is popular in PCB assembly and manufacturing due to its high activity and ease of removal with distilled water.
Depending on the requirements, water-soluble flux can contain halides, which increase the activity, therefore making them more effective and corrosive. They are as follows:
- Halide-free – used when trying to avoid halide contamination. Commonly used in military and aviation applications;
- Halide activated (low pH) – these are very active and corrosive. Due to having low pH, they are very acidic;
- Halide activated (neutral pH) – safer and less corrosive than low pH counterparts. Often used in less demanding applications.
Due to its activity, the water-soluble flux should be removed after soldering as it can be corrosive and damage the connections in the long run.
To remove water-soluble flux residue, you can use distilled water, isopropyl alcohol, or flux removers. Regular water contains minerals, which can lead to corrosion, therefore, use distilled water to clean water-soluble flux!
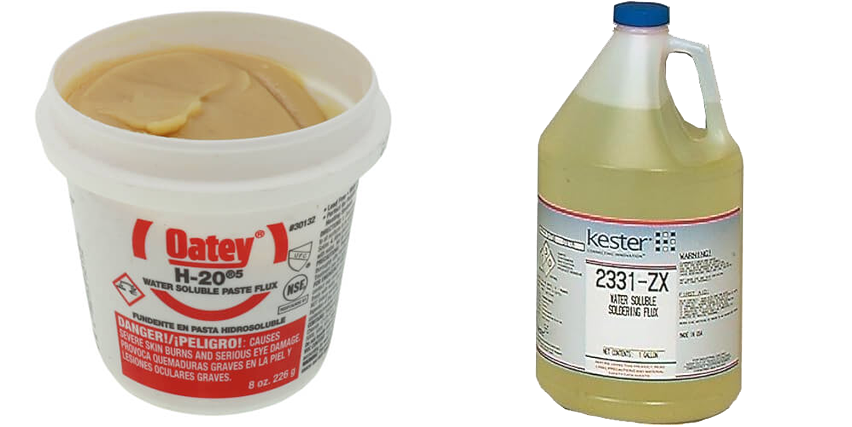
Thank you for reading our article about soldering fluxes used in electronics. If you have any questions, please leave a comment, and we’ll get back to you as soon as possible. Make sure to follow us on social media to keep in touch and learn more about the amazing world of electronics!
Leave a Reply